If you’d never heard of it before, you could be forgiven for thinking that the Continental Contidrom was one of those vast arenas that’s famous for hosting huge music events. Well, the Contidrom is vast and to some, the sounds it produces are somewhat musical, but this is the state-of-the-art tyre test facility at Continental Tyres in Jeversen near Hannover in Germany.
On arrival at the site, which was first opened in 1967, you can’t help but be impressed. It’s a multi-million-euro complex and contains just about everything the Continental boffins need to make sure its tyres are as technologically advanced, safe and economical as they can be. From outdoor test tracks, where real, professional humans (usually highly-trained former motorsport drivers) test tyres to their limits, to relatively anonymous-looking buildings that contain test equipment which will analyse the performance of tyres in just about any situation you can imagine – and some you can’t.
Continental is at the cutting edge of tyre development, and to showcase how much tyres have developed in just 10 years, we’ve been comparing the Continental Tyres SportContact 7’s wet performance against ContiSport Contact 2s, a tyre that’s been in production for over a decade.
Wet road handling
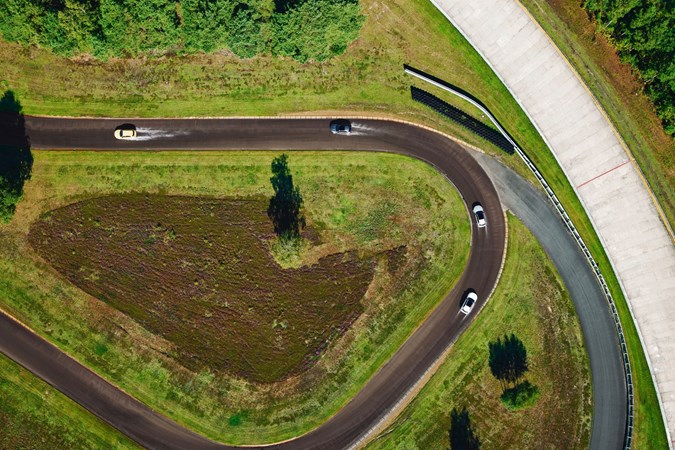
So firstly, we set out to the 1.8K-long wet handling course, which contains several 90-degree bends, including a notorious “dog-tail curve”. The entire track is watered evenly by sprinklers.
To compare older tyre technology with that of today, a selection of VW Golf GTIs were fitted with ContiSport Contact 2 tyres which have been around for more than a decade now. We made a few laps of the circuit, going faster each time, with the ContiSports giving a solid performance. The grip would be lost when they were really pushed, but all in all, they felt safe and gave a pretty impressive performance.
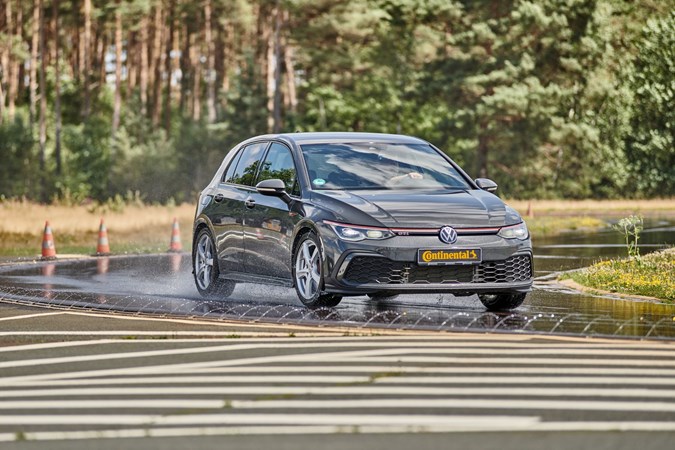
We then swapped over to another set of GTIs, this time fitted with the Continental SportsContact 7, launched in the Autumn of 2021. Where the previous tyres had started to lose their grip at certain points on the track, these just kept on holding on. After a few circuits of the track, it became pretty obvious just how far tyre tech has come. There will be a limit to what these can handle, but I was too much of a coward to be able to take them there.
Tread depth and safety
Of course, tyre condition must play its part too. This was hammered home in the braking exercise. They set up three Cupras for us to drive, each running on Continental Premium Contact 7 tyres. The first vehicle was running on brand-new tyres, the second had a tread depth of 3mm, and the third was at the legal limit of 1.6mm.
We were told to drive the cars at 85kph (53mph) onto the wet braking track. At the marker cones, we had to make an emergency stop, and the onboard computer calculated our stopping distances. The results were quite an eye-opener. The brand-new tyres stopped, on average, in 23m; the 3mm tyres averaged 28m, while the 1.6mm tyres took an average of 32m to stop. The kind of result you might expect, but what that means, is that when the car with the brand-new tyres had come to a complete stop, the car with the 3mm tread was still doing 22mph, and the 1.6mm tread was still doing 26mph. Those kinds of distances could have a huge impact on the outcome of situations that might require emergency braking.
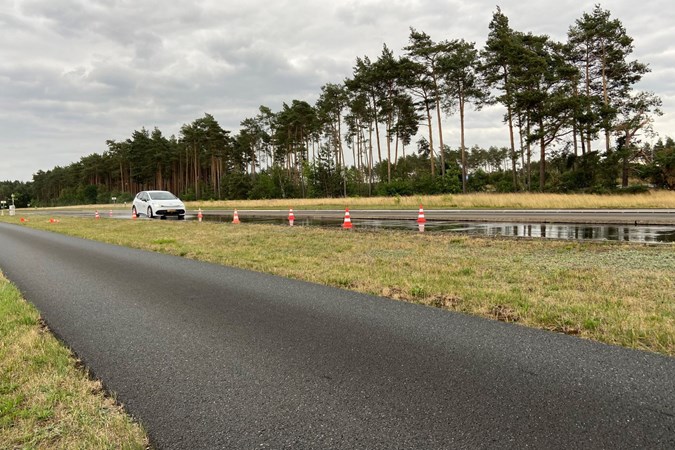
Pete Robb is Continental’s Marketing Director in the UK. He had an interesting (if not slightly tongue-in-cheek) analogy: “If someone visits a garage and they are offered a choice of either a budget or a premium tyre, some people are likely to pick the budget brand. However, if you were going on a skydive and you were offered the budget or premium parachute, your response might be different.” Those four bits of rubber are the car’s only contact with the road surface. They need to grip onto that surface to allow you to accelerate, brake and steer safely while maintaining good fuel efficiency.
That task is becoming more complicated these days with the evolution of electric vehicles, which, due to their bigger batteries, tend to weigh significantly more than their petrol or diesel-powered cousins. There’s another difference: electric vehicles have a lot more torque which means those tyres need to be able to transfer that power from the engine to the road much more quickly. Over the past few years, Continental has been working hard to make sure that all its new products are EV-ready.
The future
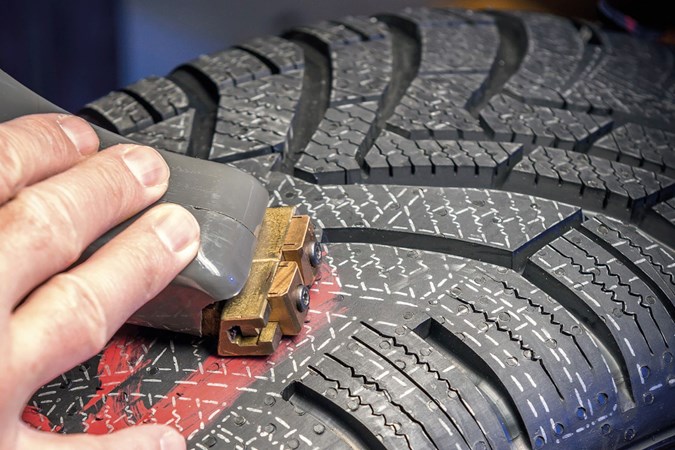
But the story doesn’t end there. They are constantly working at their research and development plant to come up with the next generation of tyres. If you can imagine a wild-haired, bespectacled scientist pouring potions from one test tube to the other, you’d get the idea. Except it’s not really like that at all. Substances, compounds, and chemicals are all mixed together in huge science kitchens before the resulting mix is delivered to experts who analyse, examine, test, and ultimately destroy the rubber to make sure it will stand up to the rigours of being used in a tyre. Once that’s done, they can make rubber circles upon which they can experiment with different tread shapes and designs. Dead easy, right? Not so much. It usually takes about three years for a tyre to be developed through this process. But that process is being sped up by the newly opened Dynamic Driving Simulator, which, believe it or not, can test tyres without the tyres actually existing! It’s all done through a very clever computer simulation system which not only speeds up the process but cuts down on the materials used in the testing process.
And now more than ever, the race is on to produce more eco-friendly tyres. The team at Continental hopes that by 2030 they’ll be using 60% sustainable materials, have a 95% waste recycling rate and a 20% reduction in water and energy use. Indeed, their newest tyre, the UltraContact NXT, uses 65% renewable and recyclable materials. The researchers are already working on the next compounds they can use, including Taraxagum – that’s dandelion sap to you and me! Who’d have thought that in the future, we might be driving on tyres made from weeds?
Alex Boyd is a Commercial Content Writer at Bauer Media writing for Parker’s and CAR and loves travel, gardening, DIY and music.
Sign up for the Parkers Newsletter to keep up to date with more of the latest reviews, news, and recommendations from the Parkers team.
Just so you know, whilst we may receive a commission or other compensation from the links on this website, we never allow this to influence product selections – read why you should trust us
Just so you know, we may receive a commission or other compensation from the links on this website - read why you should trust us.